Wie Betonblock gemacht wird - Material, Herstellung, verwendet wird, Komponenten, Struktur, Stufen, Maschinen
Hintergrund
Betonmörtel wurde von den Römern bereits 200 v.Chr. Verwendet förmige Steine zusammen in dem Bau von Gebäuden zu binden. Während der Herrschaft des römischen Kaisers Caligula, in 37-41 n.Chr.. kleine Blöcke von Betonfertigteilen wurden als Baumaterial in der Region um die heutige Neapel, Italien eingesetzt. Ein großer Teil der Betontechnologie von den Römern entwickelt wurde, nach dem Fall des Römischen Reiches im fünften Jahrhundert verloren. Erst 1824, die die englische Steinmetzen Joseph Aspdin Portland-Zement entwickelt, die eine der wichtigsten Komponenten des modernen Betons wurden.
Der erste Hohlbetonblock wurde 1890 von Harmon S. Palmer in den Vereinigten Staaten entwickelt. Nach 10 Jahren des Experimentierens, patentierte Palmer das Design im Jahr 1900. Palmer # x0027; s Blöcke waren 8 in (20,3 cm) von 10 in (25,4 cm) von 30 in (76,2 cm), und sie waren so schwer, sie hatten zu sein mit einem kleinen Kran an seinen Platz gehoben. Bis 1905 wurden die Herstellung von schätzungsweise 1.500 Unternehmen Betonblocks in den Vereinigten Staaten.
Diese frühen Blöcke wurden in der Regel von Hand gegossen und die mittlere Ausgangs betrug etwa 10 Blöcke pro Person pro Stunde. Heute Betonsteinfertigung ist ein hoch automatisierter Prozess, der bis 2000 Blöcke pro Stunde produzieren kann.
Rohes Material
Der Beton häufig verwendet, um Betonblocks zu machen, ist eine Mischung aus pulverförmigem Portland-Zement, Wasser, Sand und Kies. Dadurch entsteht eine hellgrau-Block mit einer feinen Oberflächenstruktur und eine hohe Druckfestigkeit. Ein typischer Betonblock wiegt 38-43 lb (17,2 bis 19,5 kg). Im allgemeinen hat die Betonmischung für Blöcke verwendet, um einen höheren Anteil an Sand und einen geringeren Anteil an Kies und Wasser als die Betonmischungen für allgemeine Bauzwecke verwendet. Dies erzeugt eine sehr trockene, steife Mischung, der seine Form hält, wenn sie aus der Blockform entfernt wird.
Wenn granulierte Kohle oder vulkanische Asche anstelle von Sand und Kies eingesetzt wird, wird der resultierende Block im Allgemeinen eines Schlackenblock bezeichnet. Dadurch entsteht einen dunkelgrauen Block mit einer mittleren bis grobe Oberflächenstruktur, gute Festigkeit, gute schalldämpfende Eigenschaften und ein höheren Wärmeisolationswert als ein Betonblock. Ein typischer Betonklotz wiegt 26-33 lb (11,8 bis 15,0 kg).
Die Formen und Größen von am häufigstenen Betonblöcken wurden standardisiert einheitliche Gebäudekonstruktion zu gewährleisten. Die häufigste Blockgrße in den Vereinigten Staaten, wird als ein 8-mal-8-mal-16-Block, mit den Soll-Messungen von 8 in (20,3 cm) hoch mal 8 in (20,3 cm) tief von 16 in (40,6 cm) breit. Diese nominale Messung beinhaltet Raum für eine Perle von Mörteln, und der Block selbst misst tatsächlich 7,63 in (19,4 cm) hoch von 7,63 in (19,4 cm) tief von 15,63 in (38,8 cm) breit.
Viele progressive Block Hersteller bieten Variationen des Basisblock einzigartige visuelle Effekte zu erzielen oder wünschenswert strukturelle Merkmale für spezielle Anwendungen zur Verfügung zu stellen. Zum Beispiel bietet ein Hersteller einen Block speziell Wasserleckage durch Außenwände zu widerstehen. Der Block beinhaltet eine wasserabweisende Beimengung des Betons # x0027 zu reduzieren; s Absorption und Durchlässigkeit, eine abgeschrägte Oberkante Wasser weg von der horizontalen Mörtelfuge zu vergießen, und eine Reihe von inneren Nuten und Kanäle die Strömung eines Risses induzierten zu lenken Leckage von der Innenfläche entfernt.
Ein weiterer Block-Design, ein Split-faced Block genannt, enthält eine grobe, steinartige Textur auf der einen Seite des Blocks statt einer glatten Fläche. Dies gibt dem Block das architektonische Erscheinungsbild eines Schnittes und gekleidet Stein.
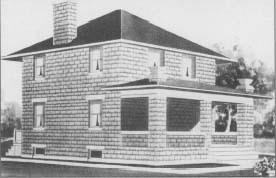
Ein Foursquare-Haus-Design, in der x0027 Architectural Company Nr Radford erscheinen; s 1908 Katalog Cement Häuser und wie sie zu bauen. Es war einer von Hunderten von cancrete Blockhaus-Design von der Radford angeboten. Sie schätzten, dass dieser Entwurf für etwa 2.250,00 $ gebaut werden kann, viel weniger als herkömmliches Steinmauerwerk Häuser der Zeit.
(Aus den Sammlungen von Henry Ford Museum # X0026; Greenfield Village.)
Betonsteine wurden zum ersten Mal in den Vereinigten Staaten als Ersatz für Stein oder Holz in dem Bau von Häusern verwendet. Das früheste bekannte Beispiel eines Haus in diesem Land war im Jahr 1837 auf Staten Island, New York komplett aus Betonstein gebaut. Die Häuser gebaut von Betonsteinen zeigten eine kreative Verwendung von gewöhnlichen kostengünstigen Materialien hergestellt wie die teurer und traditionelle Holzwerksteinmauerwerk Gebäude zu suchen. Diese neue Art der Konstruktion wurde eine beliebte Form des Wohnungsbaus in den frühen 1900er Jahren durch die 1920er Jahre. Hausbekleidung, die oft als „modern“ zu der Zeit, reichte von Tudor zu Foursquare, Colonial Revival im Bungalow. Während viele Häuser die Betonblöcke wie die Struktur als auch die Außenwandfläche verwendet wird, verwendet, um andere Häuser Stuck oder andere Beschichtungen auf der Blockstruktur. Hunderttausende dieser Häuser wurden vor allem in den Mittleren Westen der Staaten gebaut, wahrscheinlich, weil die Rohstoffe benötigt, um Betonblöcke zu machen in reichlichen Versorgung in Sandbänke und Kiesgruben in dieser Region waren. Die Betonblöcke wurden mit Gesicht Designs gemacht Stein Texturen zu simulieren: Rock-faced, Granit Gesicht, oder rusticated. Zunächst ein experimentelles Material betrachtet, Häuser von Betonsteinen gebaut wurden in vielen Portland-Zement-Herstellern # x0027 beworben; Kataloge als „feuerfeste, Ungeziefer fest und wetterfest“ und als kostengünstiger Ersatz für die immer knappe Lieferung von Holz. Viele andere Arten von Gebäuden wie Garagen, Silos und Postämter wurden gebaut und fortgesetzt werden, da diese Qualitäten dieser Bauweise gebaut werden heute.
Wenn die Hersteller einen neuen Block entwerfen, müssen sie berücksichtigen nicht nur die gewünschte Form, sondern auch den Herstellungsprozess erforderlich ist, um diese Form zu machen. Formen, die erforderlich
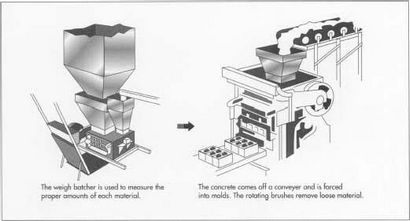
die Herstellung
Verarbeiten
Die folgenden Schritte werden häufig verwendet, Betonblöcke herzustellen.
- 5 Wenn die Last des Betons gründlich gemischt, wird sie in einer geneigten abgeladen
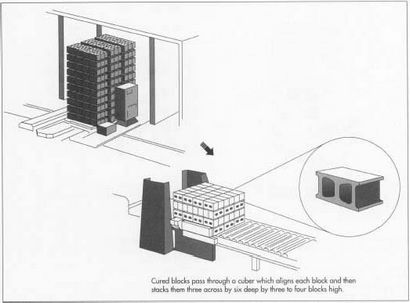
- Die Paletten 9 der Blöcke werden einem automatisierten Stapel oder Lader befördert, die sie in einem aushärtenden Gestell platziert. Jedes Rack verfügt über mehrere hundert Blöcke. Wenn eine Zahnstange voll ist, wird es auf einen Satz von Schienen gewalzt und in einen Härteofen.
10 Der Ofen ist ein geschlossene Raum mit der Kapazität mehr Racks von Blöcken zu einer Zeit zu halten. Es gibt zwei grundlegende Arten von Härten Brennöfen. Die häufigste Art ist ein Niederdruck-Dampfofen. In dieser Art werden die Blöcke in dem Ofen für eine bis drei Stunden bei Raumtemperatur gehalten, damit sie leicht härten. Dampf wird dann eingeführt, die Temperatur allmählich bei einer kontrollierten Rate von nicht mehr als 60 # xb0 zu erhöhen; F pro Stunde (16 # xb0; C pro Stunde). F (66-74 # xb0;; C) Standard Gewichtsblocks werden in der Regel bei einer Temperatur von 150-165 # xb0 gehärtet, während leichten Blöcke bei 170-185 # xb0 ausgehärtet werden; F (77-85 # xb0; C). Wenn die Härtungstemperatur erreicht ist, wird der Dampf abgeschaltet wird, und die Blöcke sind erlaubt für 12-18 Stunden in der heißen, feuchten Luft zu tränken. Nach dem Einweichen werden die Blöcke, die durch Absaugen der feuchte Luft getrocknet und weiter die Temperatur im Ofen zu erhöhen. Der gesamte Aushärtungszyklus dauert etwa 24 Stunden.
Eine andere Art von Ofen ist der Hochdruck-Dampfofen, manchmal ein Autoklav genannt. F (149-191 # xb0;; C) in dieser Art, wird die Temperatur auf 300-375 # xb0 erhöht, und der Druck wird auf 80 bis 185 psi erhöht (5,5 bis 12,8 bar). Die Blöcke sind erlaubt für fünf bis 10 Stunden einweichen. Der Druck wird dann rasch entlüftet, der die Blöcke verursacht schnell ihre eingeschlossene Feuchtigkeit zu befreien. Der Autoklav Härtungsprozess erfordert mehr Energie und einen teurer Ofen, aber es kann Blöcke in kürzerer Zeit produzieren.
- Die Zahnstangen 11 von gehärteten Blöcke werden aus dem Brennofen gerollt und die Paletten der Blöcke sind entstapelt und auf einem Kettenförderer platziert. Die Blöcke werden die Stahlpaletten abgestoßen, und die leeren Paletten werden zurück in die Block-Maschine zugeführt, um einen neuen Satz von Formblöcken zu empfangen.
- Wenn die Blöcke 12 bestehen in Split-face-Blöcke werden, werden sie zunächst geformt, wie zwei Blöcke miteinander verbunden werden. Sobald diese Doppelblocks ausgehärtet werden, durchlaufen sie einen Splitter, der sie mit einer schweren Klinge entlang des Abschnitts zwischen den beiden Hälften anschlägt. Dies bewirkt, dass der Doppelblock auf einer Fläche von jedem Stück eine raue, steinartige Textur zu brechen und bilden.
- Die Blöcke 13 durchlaufen einen cuber die jeden Block ausgerichtet ist, und dann stapelt sie in einen Würfel drei Blöcke von über sechs Blöcke tief durch drei oder vier Blöcke hoch. Diese Würfel werden außen mit einem Gabelstapler und eingelagert getragen.